Automation in industries is revolutionizing the way businesses operate, from manufacturing to logistics. This transformative process involves the integration of automated systems and technologies to streamline workflows and enhance efficiency. Historically, automation has evolved from simple mechanization to complex systems encompassing robotics, software, and artificial intelligence. Understanding the benefits, challenges, and future trends of automation is crucial for businesses looking to adapt and thrive in the modern landscape.
The adoption of automation in industries has been driven by the need to increase productivity, reduce costs, and enhance safety. Different types of automation, like robotic systems and software-based solutions, are utilized in various sectors, each tailored to specific requirements and objectives. This shift toward automation presents both exciting opportunities and potential challenges that need careful consideration.
Introduction to Automation in Industries
Industrial automation encompasses the use of technology to control and manage industrial processes with minimal human intervention. This encompasses a wide range of applications, from simple automated machinery to complex integrated systems. Automation significantly impacts efficiency, productivity, and safety within industrial settings.The core concept is to replace or augment human labor with machines and software, aiming for consistency, accuracy, and higher output in various production stages.
This trend has been accelerating, particularly with advancements in computing power, robotics, and sensor technology.
Historical Evolution of Automation
Automation’s journey has been marked by incremental advancements across diverse sectors. Early forms emerged in the textile industry with the mechanization of weaving looms in the 18th century. The 20th century witnessed a surge in automation, primarily in manufacturing, driven by the need for increased production and efficiency during the Industrial Revolution and World War II. The development of programmable logic controllers (PLCs) and computer numerical control (CNC) machines marked a pivotal shift.
More recently, the rise of digital technologies and the internet of things (IoT) has enabled further integration and sophistication in automation systems. This integration has led to a greater emphasis on data analysis and real-time feedback loops.
Key Principles of Automation Systems
Automation systems are built on several fundamental principles. These include: control systems that monitor and adjust processes; feedback mechanisms that allow for corrective actions; programmable logic that defines and executes operations; and sensors for collecting data from the environment. A crucial aspect is the integration of these components to form a cohesive and efficient system. For instance, a robotic arm in an assembly line relies on sensors to detect parts, actuators to move the arm, and a control system to coordinate the entire process.
Different Types of Automation Across Industries
Different types of automation cater to various industrial needs. The table below provides a comparative overview of robotic and software-based automation across industries.
Industry | Robotic Automation | Software-Based Automation |
---|---|---|
Manufacturing | Automated assembly lines, robotic welding, material handling, pick-and-place operations. Examples include automotive assembly plants utilizing robots for painting and welding. | Enterprise resource planning (ERP) systems, automated order processing, inventory management software, and quality control software. Examples include systems used to manage supply chains and track production. |
Logistics | Automated guided vehicles (AGVs), automated storage and retrieval systems (AS/RS), and robotic sorting systems. Examples include warehouses employing AGVs for transporting goods. | Warehouse management systems (WMS), route optimization software, and order fulfillment software. Examples include platforms that track shipments and predict delivery times. |
Healthcare | Robotic surgery systems, automated dispensing systems, and automated patient monitoring. Examples include the use of robotic arms for minimally invasive surgeries. | Electronic health records (EHR) systems, automated appointment scheduling, and billing software. Examples include systems that manage patient data and streamline administrative tasks. |
Benefits of Automation in Industries
Automation in industries is rapidly transforming production processes, offering a multitude of advantages. These benefits extend across economic gains, environmental sustainability, and enhanced worker safety and well-being. By streamlining operations and optimizing resource utilization, automation fosters significant improvements in various sectors.
Economic Advantages
Automation’s impact on the bottom line is substantial. Reduced labor costs, increased output, and improved efficiency contribute to substantial economic gains. Companies often experience lower operational expenses due to automated systems requiring less direct human intervention and lower maintenance costs over the long term. Furthermore, automation can drive productivity gains by enabling 24/7 operation, reducing downtime, and improving precision in manufacturing processes.
The enhanced output allows businesses to meet market demands more effectively and potentially achieve greater profitability.
Environmental Benefits, Automation in industries
Automation can play a pivotal role in mitigating environmental impact across diverse industries. For example, in manufacturing, automated systems can optimize material usage, minimizing waste and reducing the overall environmental footprint. Similarly, in logistics, automated transportation systems, like driverless trucks, can reduce fuel consumption and emissions, contributing to a cleaner environment. Moreover, automated processes often enable the use of more sustainable materials and manufacturing techniques, further lessening the industry’s environmental burden.
Worker Safety and Well-being
Automation significantly enhances worker safety by removing human operators from hazardous environments. This is particularly crucial in industries like mining and chemical processing. Furthermore, automated systems can handle repetitive or physically demanding tasks, alleviating strain on workers and potentially reducing workplace injuries. By taking over strenuous work, automation empowers workers to focus on higher-level tasks, contributing to greater job satisfaction and improved overall well-being.
Productivity Improvements in Specific Industries
Automation significantly boosts productivity in numerous industries. In manufacturing, automated assembly lines can drastically increase production speed and precision, reducing errors and improving output quality. This is evident in automotive manufacturing, where automated robots handle complex assembly tasks, leading to increased production volumes and quicker turnaround times. Similarly, in logistics, automated warehousing systems and robotic sorting technologies dramatically increase the efficiency of order fulfillment, enabling faster delivery times and improved customer satisfaction.
The adoption of automated systems facilitates efficient material handling, reduces manual errors, and minimizes bottlenecks in the supply chain. These examples highlight how automation contributes to greater productivity and improved operational efficiency in various industries.
Challenges and Risks Associated with Automation
Implementing automation in industries, while offering numerous benefits, presents several challenges and risks that organizations must carefully consider. These challenges span from workforce adjustments to financial implications and technical complexities. Addressing these head-on is crucial for successful automation integration.
Automation in industries relies heavily on intricate electronic components, and understanding their specifications is crucial. A deep dive into transistor characteristics, like those detailed in Transistor Specs A Comprehensive Guide , is essential for optimizing automated systems. This knowledge is fundamental for troubleshooting and fine-tuning automated processes in various sectors.
Job Displacement Concerns
Automation frequently raises concerns about potential job displacement. While automation can increase productivity and efficiency, it can also lead to the elimination of certain roles. This necessitates proactive workforce retraining and upskilling initiatives to equip employees with the skills needed for evolving job markets. The shift towards roles requiring advanced technical skills and problem-solving abilities will be paramount.
For instance, the rise of robotic process automation (RPA) has led to a reduction in manual data entry positions in many sectors, requiring workers to transition to roles focusing on overseeing and maintaining the automated systems.
Automation in industries is rapidly evolving, with new technologies constantly pushing boundaries. A key component to these advancements is the need for reliable and affordable power sources, like those explored in Cheap Long Battery Life A Deep Dive. Improved battery life is crucial for the seamless operation of automated systems, enabling extended work cycles and reduced downtime.
This ultimately drives efficiency and cost savings within the automation sector.
Financial Investments
Implementing automation frequently demands substantial upfront financial investments. These costs encompass the purchase of equipment, software licenses, integration with existing systems, and personnel training. The return on investment (ROI) often takes time to materialize, potentially extending beyond the initial projected timeframe. Careful cost-benefit analyses and realistic timelines are essential to ensure that the automation project aligns with the organization’s financial goals.
A company installing a sophisticated robotic assembly line, for example, might incur significant capital expenditure in purchasing the robots, associated software, and infrastructure modifications.
Technical Complexities and Maintenance Needs
Automated systems often involve intricate technical configurations. Integrating them with existing infrastructure and ensuring seamless operation requires specialized expertise. Maintenance and troubleshooting of these systems can also pose challenges, potentially requiring dedicated technical staff and potentially higher operational costs. The complexity of a sophisticated automated manufacturing system, for example, could require specialized engineers to manage the system’s many components and ensure optimal performance and minimal downtime.
Maintaining these systems often demands continuous updates and upgrades, adding to the overall cost.
Cybersecurity Risks and Mitigation Strategies
Automated systems are vulnerable to cybersecurity threats, given their reliance on interconnected networks. Malicious actors could exploit vulnerabilities in these systems, leading to data breaches, system disruptions, and financial losses. Robust cybersecurity protocols and regular security assessments are essential to mitigate these risks. Companies should implement multi-factor authentication, firewalls, and intrusion detection systems to protect their automated systems.
For instance, a company using automated inventory management software might be vulnerable to hacking if the system’s security measures are not robust enough. Therefore, implementing strong security measures is critical.
Types of Automation in Industries
Industrial automation encompasses a diverse range of technologies, each with unique capabilities and applications. These technologies automate various tasks, increasing efficiency, reducing errors, and improving overall productivity. From simple repetitive tasks to complex decision-making processes, automation systems are transforming industries across the globe.
Industrial Robots
Industrial robots are programmable mechanical devices designed to perform repetitive tasks in a controlled and predictable manner. Their precise movements and capabilities make them highly valuable in manufacturing, assembly, and material handling. They are typically controlled by computer programs that define their actions and movements.
- Applications: Industrial robots are used extensively in automotive assembly lines for tasks such as welding, painting, and part placement. They are also employed in electronics manufacturing, handling delicate components with high accuracy. In the food and beverage industry, they handle packaging and sorting tasks. Furthermore, they are increasingly being deployed in warehousing and logistics for tasks like picking, packing, and loading/unloading goods.
- Types: Different types of robots exist, each tailored to specific tasks. Articulated robots, with multiple joints, are commonly used for complex manipulation. Cartesian robots, with linear axes, are well-suited for tasks requiring precise positioning, such as pick-and-place operations. SCARA (Selective Compliance Assembly Robot Arm) robots excel at assembly tasks, providing high speed and accuracy. Collaborative robots (cobots), designed for safe interaction with human workers, are gaining popularity in various industries.
Programmable Logic Controllers (PLCs)
PLCs are specialized digital computers that automate industrial processes. They act as the central control system, receiving inputs from sensors, processing the information, and controlling actuators. PLCs are widely used in automated manufacturing, process control, and building automation systems.
- Function: PLCs execute predefined instructions, based on inputs, to control machinery and equipment. They are crucial in monitoring and controlling various processes, such as temperature, pressure, and flow rates. They can also manage complex sequences of operations.
- Implementation: PLCs are programmed using specific languages, like ladder logic, which resembles electrical circuit diagrams. This makes programming relatively easy for engineers familiar with industrial control systems. The program defines the actions the PLC will take based on different sensor inputs. This control loop allows for efficient and automated operation of machines.
Machine Learning in Automation
Machine learning (ML) is transforming automation by enabling systems to learn from data and improve their performance over time. ML algorithms can be trained to recognize patterns, predict outcomes, and make decisions without explicit programming.
- Function and Implementation: In automation, ML algorithms can be used to optimize processes, predict maintenance needs, and improve quality control. For example, in manufacturing, ML can identify defects in products with high accuracy, leading to improved quality and reduced waste. In predictive maintenance, ML models analyze sensor data to anticipate equipment failures, allowing for proactive maintenance and preventing costly downtime.
Sensors and Data Analytics in Automated Processes
Sensors provide real-time data about the physical environment, enabling automated systems to respond to changes and adjust their operation. Data analytics tools then process this data, extracting insights and improving decision-making.
- Function and Implementation: Sensors monitor parameters such as temperature, pressure, flow rate, and position. These readings are crucial for monitoring and controlling automated processes. Data analytics then process this data to identify trends, anomalies, and patterns. For example, in a production line, sensors can detect variations in product quality, enabling the system to adjust parameters and maintain consistent output.
Data analytics tools can further analyze these data points to predict future trends, helping in optimizing production and reducing waste.
Future Trends in Industrial Automation
Industrial automation is constantly evolving, driven by advancements in technology and the need for greater efficiency and productivity. This evolution is poised to reshape manufacturing and production processes, creating new opportunities and challenges for businesses. Key emerging trends include the integration of advanced technologies like artificial intelligence and the cloud, ushering in a new era of intelligent and interconnected systems.The future of industrial automation promises to be more sophisticated, adaptive, and interconnected.
These advancements are not merely incremental improvements; they represent a paradigm shift, fundamentally altering how industries operate. This section delves into these evolving trends, examining their potential impacts and implications.
Emerging Technologies Influencing Industrial Automation
Several emerging technologies are poised to significantly impact industrial automation. These technologies offer solutions for enhancing efficiency, improving decision-making, and increasing the overall productivity of industrial processes. These technologies include:
- Artificial intelligence (AI): AI-powered systems are increasingly used for predictive maintenance, quality control, and process optimization.
- Internet of Things (IoT): IoT devices are connecting machines and equipment, providing real-time data for monitoring and control.
- Robotics: Collaborative robots (cobots) are becoming more prevalent, enabling increased flexibility and efficiency in production.
- 3D printing: Additive manufacturing techniques are transforming manufacturing processes, allowing for customized and complex designs.
Impact of Artificial Intelligence on Automation in the Future
Artificial intelligence is transforming automation by enabling more intelligent and adaptive systems. AI algorithms can analyze vast amounts of data to identify patterns, predict failures, and optimize processes in real-time. This capability leads to improved efficiency and reduced downtime.Examples of AI’s impact include:
- Predictive maintenance: AI algorithms can analyze sensor data from machines to predict potential failures, allowing for proactive maintenance and reducing unplanned downtime.
- Process optimization: AI can identify inefficiencies in production processes and suggest improvements, leading to increased productivity and reduced costs.
- Quality control: AI can analyze images and data to identify defects in products, improving quality and reducing waste.
Potential for Human-Machine Collaboration in Automated Systems
The future of industrial automation increasingly involves human-machine collaboration. This collaboration aims to leverage the strengths of both humans and machines, creating a more efficient and productive workforce. Humans can oversee complex tasks, make critical decisions, and handle situations requiring adaptability.
Role of Cloud Computing in Supporting Industrial Automation
Cloud computing plays a critical role in supporting industrial automation by providing a platform for data storage, analysis, and processing. The cloud allows for real-time data sharing and collaboration among different systems and departments, enabling better decision-making and improved overall efficiency.Cloud computing in industrial automation supports the following:
- Data storage and analysis: Cloud platforms can store and process large volumes of data generated by industrial machines and equipment, enabling data-driven insights.
- Real-time data sharing: Cloud systems facilitate real-time data sharing among different departments and stakeholders, enabling better coordination and decision-making.
- Remote monitoring and control: Cloud-based systems allow for remote monitoring and control of industrial equipment, enhancing efficiency and reducing downtime.
Workforce Adaptation and Training
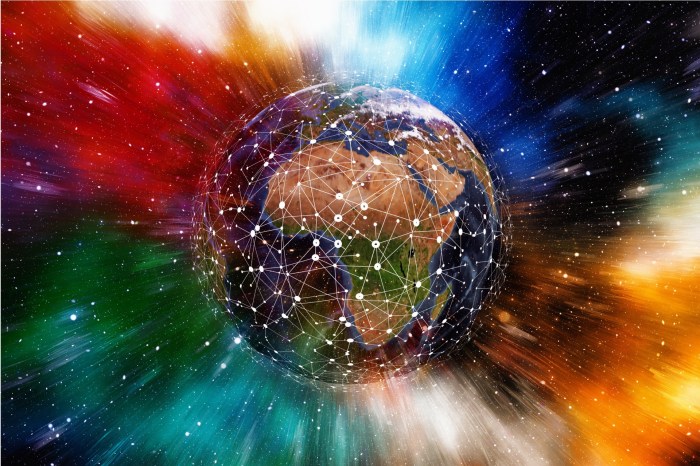
Industrial automation is reshaping the manufacturing landscape, presenting both opportunities and challenges for the workforce. Adapting to these changes requires proactive strategies for workforce development and training. Successfully navigating this transition depends on understanding the evolving skills gap and implementing effective reskilling and upskilling programs.The implementation of automation technologies often necessitates a shift in the required skillset for industrial workers.
This shift is not always seamless, and necessitates a thoughtful approach to ensure the transition is smooth and beneficial for all stakeholders. Addressing the skills gap is paramount to leveraging the benefits of automation while minimizing potential disruptions.
Skills Gap Emerging with Automation Adoption
The introduction of automation technologies necessitates a shift in the required skillset for industrial workers. Traditional manufacturing jobs are increasingly requiring a blend of technical and soft skills. The skills gap emerges when the existing workforce lacks the necessary expertise in areas like programming, data analysis, and maintenance of automated systems. Furthermore, there’s a rising need for individuals with skills in areas like robotics, artificial intelligence, and machine learning to operate and maintain these advanced systems.
For instance, workers who previously focused solely on manual tasks may now need to learn to operate and maintain robotic systems or interpret data generated by automation systems.
Training Workers for New Roles in Automated Environments
Effective training programs are crucial to bridge the skills gap and equip workers with the necessary competencies for automated environments. These programs should incorporate hands-on experience with the latest automation technologies. For example, simulated environments or pilot programs can offer workers a safe and controlled setting to practice using robotic arms, data analytics tools, or other relevant equipment.
In addition to technical skills, training should also emphasize soft skills such as problem-solving, critical thinking, and teamwork, which are essential for success in collaborative automated environments. This integrated approach prepares workers for the complexities of modern industrial settings.
Strategies for Reskilling and Upskilling the Workforce
Reskilling and upskilling initiatives are vital for enabling a smooth transition to automated environments. These programs should be tailored to the specific needs of individual industries and organizations. For instance, companies in the automotive industry may focus on training workers in robotics and automated assembly lines, while those in the food processing industry may prioritize training in automated quality control and food safety systems.
Companies should consider providing apprenticeships, online courses, and mentorship programs to facilitate the reskilling process. Further, government support and industry partnerships are crucial to ensure these initiatives are accessible and effective.
Lifelong Learning in the Age of Automation
Lifelong learning is increasingly important in the age of automation, as technological advancements necessitate continuous adaptation and skill development. Workers need to be prepared for a future where learning and development are ongoing processes. This could involve participating in online courses, attending workshops, or pursuing further education to stay current with the evolving technological landscape. Encouraging a culture of continuous learning within organizations is vital to fostering a resilient and adaptable workforce.
For instance, companies can provide incentives for employees to pursue relevant certifications or degrees, or create internal training programs that address emerging technological trends.
Ethical Considerations in Industrial Automation: Automation In Industries
Industrial automation, while offering significant benefits, presents crucial ethical considerations that must be carefully addressed. These considerations range from the impact on employment to the potential for bias in automated systems. Understanding and proactively mitigating these ethical challenges is essential for responsible automation development and deployment.
Employment Implications of Automation
The widespread adoption of automation raises concerns about job displacement. While automation can create new roles, it also necessitates retraining and upskilling initiatives to equip workers with the skills needed for emerging job markets. A strategic approach to workforce adaptation is critical for minimizing the negative impact on employment and fostering a more inclusive transition. This requires a proactive and forward-thinking approach to education and training, preparing individuals for the evolving demands of the automated workforce.
Responsible Automation Development
Developing and deploying automated systems responsibly necessitates a multi-faceted approach. Ethical guidelines and frameworks should be established to ensure that automation is used for the betterment of society, minimizing potential harm. This includes prioritizing human well-being, safety, and fairness in the design and implementation of automated processes. Transparency in automation decisions and processes is also critical to building trust and accountability.
Potential Biases in Automated Systems
Automated systems, trained on data sets, can inherit and perpetuate existing societal biases. This can lead to discriminatory outcomes in areas like hiring, loan applications, or even criminal justice. For example, facial recognition algorithms trained primarily on data from one demographic might perform less accurately on individuals from other groups. Therefore, rigorous testing and validation are crucial to identify and mitigate potential biases in automated systems, ensuring fairness and equity in their applications.
Ethical Guidelines for Automation Development
Implementing ethical guidelines is crucial for ensuring the responsible development and deployment of automated systems. These guidelines should cover various aspects, from data privacy to algorithmic transparency. Adherence to these guidelines will help to mitigate risks and foster public trust.
Category | Specific Guidelines | Rationale |
---|---|---|
Data Collection and Use | Obtain informed consent for data collection; ensure data security and privacy; avoid collecting sensitive data without justification. | Protecting personal information is paramount. Data should be collected and used responsibly and ethically. |
Algorithmic Transparency and Explainability | Design algorithms that are understandable and explainable; make decision-making processes transparent; avoid “black box” systems. | Transparency fosters trust and allows for scrutiny of the decision-making process. This is crucial for identifying and addressing potential biases. |
Bias Mitigation and Fairness | Rigorously test automated systems for bias; actively address and mitigate identified biases; promote fairness and equity in outcomes. | Ensuring fairness in outcomes is essential for avoiding discriminatory outcomes and building public trust. |
Human Oversight and Control | Maintain human oversight in critical decision-making processes; ensure that humans retain control in situations requiring judgment and critical thinking. | Maintaining human oversight and control is vital to ensuring accountability and mitigating potential risks. |
Case Studies of Successful Automation Implementations
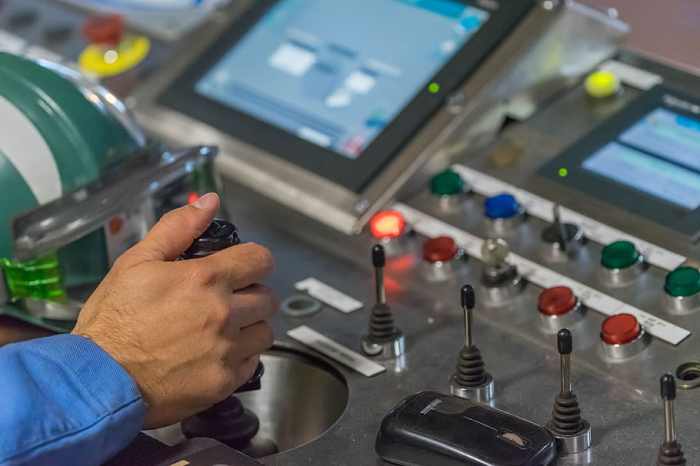
Implementing automation successfully requires careful planning, execution, and ongoing adaptation. These case studies showcase real-world examples of how automation has been successfully integrated into various industries, demonstrating the tangible benefits and addressing potential challenges. Understanding these implementations provides valuable insights for future automation projects.
Automotive Manufacturing
Automotive manufacturing has been a pioneer in automation, driven by the need for efficiency and quality control. Successful implementations often involve robotic welding, painting, and assembly lines, reducing human error and increasing production speed. These systems can be highly complex, requiring significant upfront investment and meticulous integration with existing processes.
Company | Automation Implementation | Positive Outcomes | Lessons Learned |
---|---|---|---|
Toyota | Advanced robotic assembly lines and predictive maintenance systems | Reduced production time by 20%, improved quality by 15%, and minimized downtime by 10%. | Early and thorough training for workers on new technologies and protocols is critical for successful implementation. |
Ford | Automated material handling systems and AI-powered quality control | Increased output by 25% and significantly reduced material waste. | Effective communication and collaboration between automation specialists and production teams are essential to seamless integration. |
Warehousing and Logistics
The warehousing and logistics sector benefits significantly from automation, especially in handling large volumes of goods. Automated guided vehicles (AGVs), robotic picking systems, and warehouse management systems (WMS) are frequently employed. These technologies optimize order fulfillment and streamline supply chains.
Company | Automation Implementation | Positive Outcomes | Lessons Learned |
---|---|---|---|
Amazon | Extensive use of robots, drones, and automated sorting systems | Reduced order fulfillment time by 30%, increased efficiency by 40%, and improved customer satisfaction through faster delivery. | Scalability and adaptability of the automation system are crucial to handle fluctuating order volumes and changing demands. |
DHL | Automated sorting centers and real-time tracking systems | Reduced labor costs by 15%, improved accuracy in order processing by 10%, and enhanced visibility for customers. | Implementing robust data security and disaster recovery measures is vital for safeguarding sensitive logistical information. |
Food and Beverage Processing
Automation is crucial for maintaining consistent quality and output in food and beverage processing. Robots are used for tasks such as packaging, labeling, and quality inspection. The safety and hygiene requirements in this industry demand careful design and maintenance of automated systems.
Company | Automation Implementation | Positive Outcomes | Lessons Learned |
---|---|---|---|
Nestlé | Automated packaging lines and quality control systems | Improved product consistency, reduced production costs by 8%, and minimized contamination risks. | Ensuring compliance with food safety regulations throughout the automation process is paramount. |
PepsiCo | Robotic sorting and labeling systems | Increased production speed by 10%, improved accuracy in product labeling by 15%, and enhanced efficiency in handling diverse product lines. | Regular maintenance and calibration of automated systems are essential to guarantee quality and consistency. |
Global Perspectives on Industrial Automation
Industrial automation is rapidly transforming manufacturing landscapes worldwide. Understanding the varying approaches and challenges across different nations is crucial for businesses seeking to navigate this evolving global landscape. Diverse factors, including technological readiness, government support, and cultural norms, shape automation adoption patterns.A comparative analysis of automation practices in various countries reveals substantial differences in implementation strategies. These variations are driven by a complex interplay of factors, including economic development levels, infrastructure capabilities, and workforce demographics.
The impact of these factors is further amplified by government policies and incentives that either encourage or hinder automation adoption. Understanding these nuances is essential for informed decision-making and strategic planning in the globalized manufacturing sector.
Comparison of Automation Practices in Different Countries
Different nations exhibit varying approaches to industrial automation, reflecting diverse economic, social, and technological contexts. Advanced economies often prioritize advanced robotics and sophisticated software systems, while developing nations might focus on more basic automation solutions, particularly in sectors with high labor costs. This difference in approach necessitates adaptable strategies for international businesses.
Impact of Government Policies on Automation Adoption
Government policies play a significant role in shaping automation adoption rates within a country. Incentives, such as tax breaks for automation investments or funding for research and development, can significantly encourage automation adoption. Conversely, regulations related to labor standards or environmental protection can impact the feasibility and desirability of certain automation technologies. Furthermore, policies related to workforce retraining and upskilling can help mitigate potential job displacement concerns.
Examples of International Collaborations in Automation Research
International collaborations are vital for driving innovation in industrial automation. Joint research projects between universities and companies across borders often lead to the development of cutting-edge technologies. These collaborations facilitate the exchange of expertise, fostering a more comprehensive understanding of automation challenges and solutions. The sharing of knowledge and resources enhances global capabilities in this rapidly evolving field.
Comparison of Automation Adoption Rates Across Major Economies
Economy | Automation Adoption Rate (estimated percentage) | Key Drivers | Challenges |
---|---|---|---|
United States | 65% | Strong R&D investment, advanced infrastructure, skilled workforce | Labor shortages, supply chain disruptions |
Germany | 70% | Strong vocational training, emphasis on Industry 4.0, robust manufacturing sector | High initial investment costs, adapting to changing technologies |
China | 55% | Massive investment in infrastructure, large manufacturing base, government support | Maintaining worker skills, environmental concerns |
Japan | 80% | Long history of automation, strong robotics sector, high technological capability | Maintaining competitiveness, adapting to demographic changes |
South Korea | 75% | Focus on advanced manufacturing, strong semiconductor industry, skilled workforce | Dependence on global supply chains, managing technological disruptions |
Note: Adoption rates are estimated and can vary depending on the specific industry and criteria used for measurement. The table provides a general overview.
Final Wrap-Up
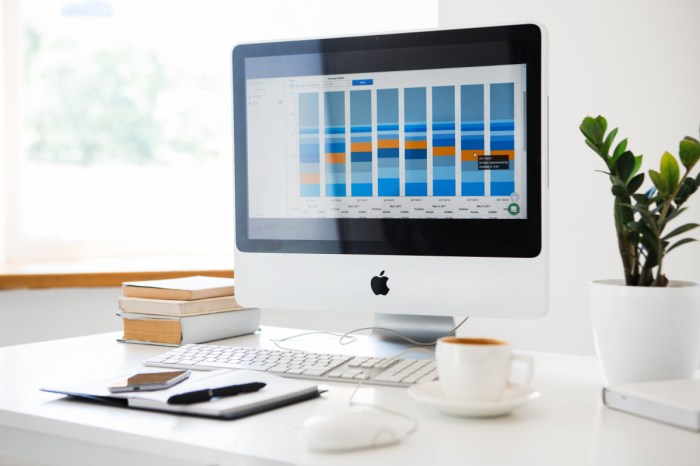
In conclusion, automation in industries is a dynamic field with a profound impact on the global economy. The advantages of increased efficiency, safety, and productivity are undeniable. However, the challenges of job displacement, financial investment, and technical complexities must be carefully addressed. The future of industrial automation hinges on our ability to adapt, innovate, and develop ethical frameworks for responsible implementation.
Ultimately, a harmonious integration of human and machine capabilities is key to realizing the full potential of this transformative technology.
Detailed FAQs
What are some common misconceptions about automation in industries?
Many believe automation solely leads to job losses. While some roles may change, automation often creates new opportunities and requires workers to adapt to new skills. Furthermore, automation can improve working conditions and allow humans to focus on more complex tasks.
How can businesses effectively manage the transition to automation?
A phased approach, focusing on pilot projects and comprehensive training, can help businesses manage the transition smoothly. It’s crucial to involve employees in the planning process and provide the necessary support and resources for adaptation.
What are the most significant environmental benefits of industrial automation?
Automation can reduce resource consumption, minimize waste, and optimize energy usage in many industries. Improved efficiency often leads to lower emissions and a smaller environmental footprint.